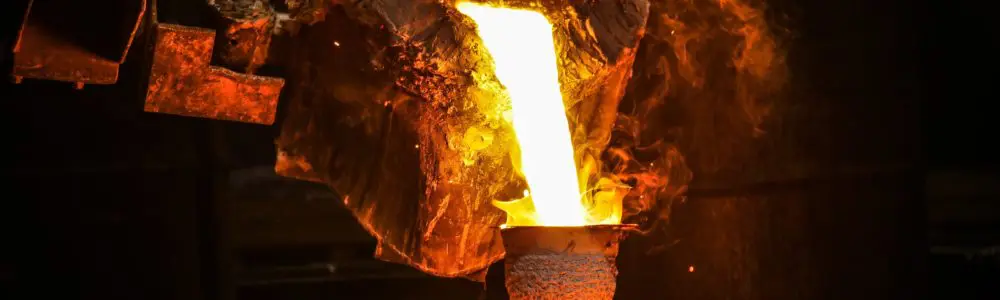
Machined Investment Castings
Investment Castings are known for their high quality, intricate details, complex shapes, accurate dimensions and smooth surfaces. But did you know that investment castings typically require much less machining and other post-cast processing than conventional castings or fabricated components? This makes machined investment castings a good choice for design engineers looking for high-strength and lightweight components with reduced lead times, waste and energy costs.
What are Machined Investment Castings?
Although achieving “net-shape” or “near-net-shape” cast components drastically reduces secondary processing costs, some engineers require machined investment castings due to precise dimensional requirements, tight tolerances, specialty profiles, tapped holes, etc. Typically, standard investment casting tolerances are +/-0.010” for the first inch and +/- 0.005” for each succeeding inch. During the design for manufacturing process, Investment Casting engineers can reduce or eliminate machining previously required on sand castings, fabrications or forgings. If machining is still needed, the machining requirements of an investment casting will be less than for sand castings or welded fabrications.
What is the Investment Casting Process?
The name investment casting is derived from the process of a pattern being “invested” or surrounded with a refractory material to create a mold. The pattern, made of wax or a 3D printed material, is melted away to create a hollow cavity in the mold into which molten metal is poured. Investment castings can weigh anywhere from a few ounces to several hundred pounds.
Types of Machined Investment Castings
The type of machining process needed varies depending on how the machined investment castings will be used. For example, the aerospace and power generation industries use machined investment castings for many safety-critical applications that require high-strength in extreme environmental conditions. In these industries, it is important to ensure strict tolerances are achieved by casting and machining the metal components to exact specifications.
Different machining equipment and tooling is used to achieve a part’s final configuration. These machining processes include:
Turning – A single edge cutting tool is used to remove excess material from a rotating component to create a cylindrical shape.
Drilling – A round hole is created in the casting.
Boring – A single point tool is used to improve the accuracy of an already roughly made hole.
Reaming – A small amount of metal is removed from an already drilled hole to achieve a tighter finished tolerance.
Milling – A rotating tool with several cutting edges creates a straight surface.
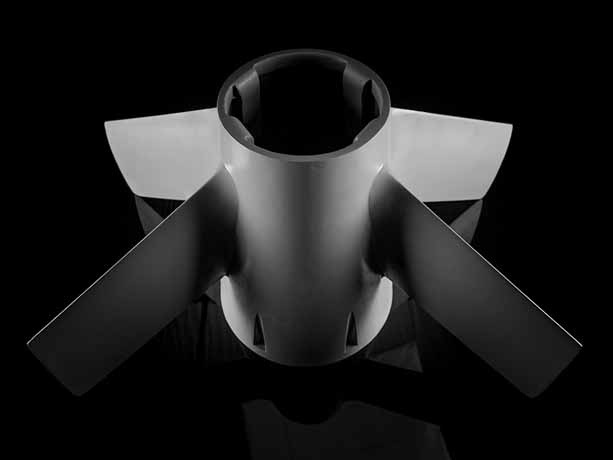
The Benefits of Machined Investment Castings
When it comes to making high-quality metal components, machined investment castings can provide a high return on your investment! Used for thousands of years, the investment casting or lost-wax process is now the future of manufacturing. Here’s just a few of the benefits:
- Less Waste and Cost: With the escalating cost of metals or alloys, fabricating parts out of bar metal can be expensive, especially if they require extensive machining. Turning a fabrication into an investment casting eliminates metal scrap which represents significant savings in alloy cost. Considering current shortages in metals, investment casting may be the only way to economically manufacture the part. Today’s competitive labor market is also creating soaring costs and production challenges.
- Design Flexibility: As opposed to forming parts from bar metal, machined investment castings can be used to convert multi-piece fabrications into one-piece castings, greatly reducing lead-times, waste and cost. In addition, machined investment castings offer a myriad of metals including low cost alloys such as carbon and tool steels or costly alloys such as aluminum, stainless steel, hastalloy, cobalt and Inconel.
- Intricate Shapes/Thin Walls: Also known as “precision casting”, the investment casting process produces components with intricate and complex shapes, superb surface finishes and strict dimensional accuracy.
- Environmentally Friendly: Investment Casting is a totally earth-friendly process. Metals and wax used in manufacturing are recycled and reused to make new parts. Although the ceramic shell material cannot be recycled within the investment casting process, it is classified as an inert substance and controlled landfill disposal is not necessary. Waste from ceramic slurry can also be recycled for many uses including fill for construction projects or filler for concrete.
Machined Investment Castings from Barron Industries
Barron Industries is a global supplier of precision cast parts, machined components and complete assemblies. Barron manufactures highly-engineered investment castings with both ferrous and non-ferrous metals. Using the most advanced casting and CNC machining technology, Barron’s start-to-finish manufacturing process includes everything from design for manufacturing to in-house Nadcap certified NDT and welding, as well as off-shore production and complete supply chain management.