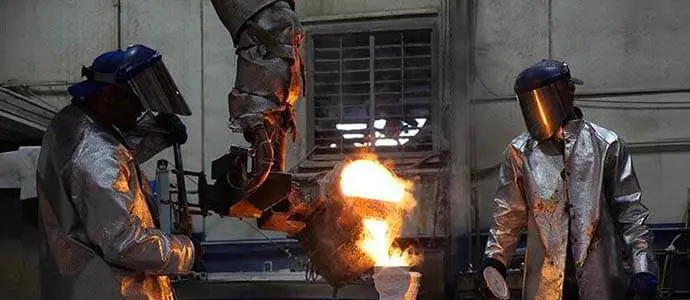
Investment Casting Defects & Discontinuities
Although investment casting is an efficient and reliable way to create metal components, casting defects are not uncommon. In fact, even the best foundries occasionally create castings with defects. Read on to learn more about the various types of defects, how to prevent them, and how to fix them.
Types of Casting Defects
The two most common types of casting defects are porosity and shrinkage defects. Throughout the investment casting process, it’s possible for other defects to occur due to cooling errors, uneven pouring, and more. Keep reading to learn more about the many defects that can occur during the casting process.
Porosity
Porosity is a measure of the void spaces in a material, and is a fraction of the volume of voids over the total volume. It is a phenomenon that occurs in materials, especially castings when the molten metal holds a large amount of dissolved gas. As a result, gas bubbles form as the material cools. Turbulence can also introduce gasses during the casting process. This occurs when the molten metal is poured too quickly into the mold. Porosity causes a casting to leak and makes it unusable for holding pressure in applications like pumps, compressors, transmissions and plumbing fixtures.
Shrinkage/Voids
Shrinkage can appear as a crack or breakage on the surface of the casting. There are two main types of shrinkage – solidification shrinkage and pattern maker’s shrinkage. Solidification shrinkage occurs because metals are less dense as liquids than solids. Pattern maker’s shrinkage occurs due to the natural shrinkage of the molten metal as it cools to room temperature. A shrinkage allowance is therefore factored into the pattern design at the start of the process. Shrinkage defects can be particularly bad, as they can cause the castings to break.
Non-Metallic Inclusions
Inclusion defects occur when foreign materials are introduced into the liquid metal through the dewaxing, metal and pouring processes. The two most common types of inclusion defects are slag inclusions and sand inclusions.
Slag is non-metallic material that is attached to the raw metal. It is actually an important part of the melting process, but it should be removed before casting. In some circumstances, slag can make it into the casting, which causes defects. Sand inclusions can occur when sand from the mold makes it into the metal itself.
Linear Indications
Linear indication defects appear on the casting as cracks, hot tears, and cold shuts. All three of these defects can impact the structural integrity of the casting, causing it to break.
Rough/decarburized surface
Some castings are considered hard to machine because of their rough or decarburized surface. However investment castings are produced using a ceramic shell molding material which is preheated before casting creating a smooth homogenous surface that is very “machining” friendly. In addition, the introduction of a reducing atmosphere immediately after casting prevents the formation of a decarburization layer on the surface of steel castings.
Although there are many defects that can occur during the casting process, there are many other ways to prevent them from happening in the first place.
How to Prevent Defects
As mentioned previously, porosity defects occur when gasses get trapped within the metal during the casting process. Barron Industries minimizes this type of defect from occurring by using various degassing techniques, including:
- Predictive Solidification Modeling
- Rollover Furnaces (Used for Thin-Walled Parts)
- Prime Virgin AOD or VOD Ingot
In general, our investment casting process is designed to prevent porosity defects. We use permeable, pre-heated ceramic shells which trap less gas and allow more air to escape during the process.
Preventing Shrinkage & Void Defects
Barron Industries also uses predictive solidification modeling to prevent the formation of shrinkage cavities in castings. We also ensure that we have tight control of the gating, risering, temperature, and flow rates to ensure better quality. Lastly, we use chill paint, exothermic hot toppings, and insulating wrap materials to eliminate shrinkage/void defects.
Avoiding Inclusion Defects
Inclusions are common defects that often occur during the dewaxing, metal, and pouring processes. Barron Industries avoids inclusion defects during the casting process by using automated temperature and humidity control in its ceramic shell molding operations.
We also couple this prevention technique with daily ceramic slurry testing and adjustments; this ensures that we are creating a shell that is uniform and strong enough to withstand the rigors of the We also couple this prevention technique with daily ceramic slurry testing and adjustments; this ensures that we are creating a shell that is uniform and strong enough to withstand the rigors of the dewaxing cycle without breaking. Our techniques also prevent ceramic inclusion defects during the pouring process.
At Barron Industries, we also use deoxidizing materials and techniques to coagulate any non-metallic material prior to tapping metal from the furnace. Our process engineers also design special ceramic filters that prevent even the smallest inclusions during the casting process.
Cracks, Cold Shuts, & Other Linear Indication Defects
We also use prevention solidification modeling and other “clean metal” techniques to prevent most linear indication defects, including cracks, hot tears, and cold shuts. Before we finish the casting process, we also use our NADCAP-certified in-house Fluorescent Penetrant Inspection and Computed Radiography technology to find any potential cracks, hot tears, or cold shuts. In the event that we do find any cracks, we repair them via welding, or we scrap the ones that cannot be fixed, so as to ensure 100% conforming material is shipped to Barron’s customers.
Get Defect – free Castings from Barron Industries
A casting should be inspected for surface defects as soon as possible. Some defects can be easily spotted without any equipment, but others will be found using the most advanced non-destructive testing techniques including Barron’s computer radiography, and penetrant testing. If you need defect-free castings, turn to Barron Industries. We’ve been helping clients in the defense, transportation, aerospace, and industrial sectors for nearly a century. When you work with us, we ensure quality from start to finish, and use state-of-the-art technology and techniques to prevent most casting defects. Call us today to learn more about our prevention techniques, or to request a quote.