347 (CF-8C) Stainless Steel
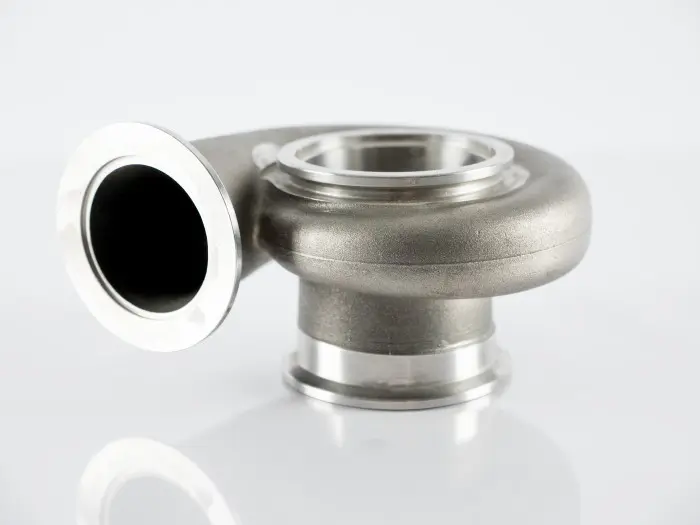
Barron Industries specialize in investment casting with 347 (CF-8C) stainless steel. Our team has the resources, knowledge, and experience needed to ensure precision components for clients in the aerospace, medical, aviation, automotive, and defense industries.
Keep reading to learn about the composition, properties, advantages, and applications of 347 CF-8C, or contact us today to request a quote.
Properties of 347 (CF-8C) Stainless Steel
Common names for this alloy include ASTM A351 grade CF8C, Type 347, AISI 347, Alloy 347, austenitic stainless steel, and UNS S34700. The physical properties of Type 347 include:
- Tensile Strength Range: 70-85,000 PSI
- Yield Strength Range: 32-36,000 PSI
- Elongation Percentage: 30 to 40%
- Rockwell Hardness Score: 90
Additionally, ASTM A351 grade CF8C stainless steel is composed of: nickel (9-11%), chromium (17-19%), sulfur (0.03% maximum), silicon (0.75% maximum), carbon (0.08% maximum), manganese (2% maximum), and phosphorus (0.045% maximum).
Advantages
Engineers and manufacturers prefer 347 stainless steel for use in high-temperature applications requiring high strength and excellent corrosion resistance. Beyond its corrosion resistance and strength, additional benefits include:
- High Creep Stress
- Can Withstand Extreme, Varying Temperatures
- Great Mechanical Properties
- Superior Weldability
Applications
347 stainless steel’s primary applications are in boiler castings, welding equipment, heating elements for furnaces, and aircraft exhaust systems. However, it has various other applications including those listed below:
- Steam Boilers
- Refractory Anchor Bolts
- Fluidized Bed Combustors
- Burners & Combustion Chambers
- Tube Hangers for Petroleum Refinement
Request a Quote Today
Have questions about casting with 347 (CF-8C) stainless steel? Contact our team at Barron Industries today.
We’ve been providing high-quality stainless steel castings to clients in many sectors since 1983. Clients continue to trust us time and time again because of our commitment to quality and accuracy. In fact, all castings that we produce are quality-tested using NADCAP-certified, non-destructive testing equipment.
Let us help you produce the precision components that you need!
Have any Questions?
Please feel free to contact us. We will get back to you within 1-2 business days. Or just call us now.